Stahl ist einer der wichtigsten Werkstoffe und eines der weltweit populärsten Baumaterialien, doch wie sieht der Prozess der Stahlherstellung aus? Diesem Thema widmen wir unseren neusten Beitrag. Daraus erfahren Sie, was Stahl eigentlich ist, wie und woraus man ihn produziert, aus welchen Etappen sich dieses Vorgehen zusammensetzt sowie einiges über die Stahlverwendung in verschiedenen Industrie- und Lebenssphären.
Denn unabhängig davon, womit man sich beschäftigt, spielt Stahl, so oder anders, eine bestimmte Rolle in unserem Leben. Man kann sich einfach keinen Bereich der menschlichen Tätigkeit vorstellen, bei dem Produkte aus diesem langlebigen, relativ kostengünstigen Material nicht verwendet werden. Wir hoffen somit, Ihnen eine Prise Kompaktwissen zum Thema Stahlherstellung zu liefern, das für Sie aus verschiedenen Gründen von Nutzen sein könnte.
Wie wird Stahl hergestellt?
Unter dem Begriff „Stahl“ versteht man sämtliche Legierungen aus Eisen und Kohle bzw. anderen Elementen, bei denen der Gehalt an Kohlenstoff 2,06-2,11 % nicht übersteigt. Bei den sog. „legierten Stählen“ (der Gegensatz dazu wäre Edelstahl) kann der Kohlenstoffgehalt höher sein. Generell sieht es so aus, dass der Anteil an hartem und sprödem Zementit (dies hängt eben vom Kohlenstoff ab) sich unmittelbar auf die Härte und Haltbarkeit des Stahls auswirkt.
Wie wird Stahl hergestellt? In der Industrie gewinnt man Stahl aus Roh- bzw. Gusseisen und Stahlschrott, den man in Europa im Rahmen des Recyclingprogramms sammelt. Das Gusseisen an sich stellt man aus Eisenerz her, einem natürlichen Konglomerat verschiedener Eisenoxide- und Sulfide. Zu den letzteren zählen:
- Limonit – braunes Eisenerz;
- Hämatit – rotes Eisenerz;
- Magnetit – magnetisches Eisenerz;
- Pyrit – Schwefelrohstoff zur Produktion von Schwefelsäure.
Roheisen schmilzt man in Hochöfen unter Verwendung von Koks, der zugleich als Brenn- und Kohlenstoffquelle dient. Bei hohen Temperaturen reduziert sich das Eisen und es entsteht dessen Legierung mit Kohlenstoff. Diese Mischung bezeichnet man eben als Gusseisen.
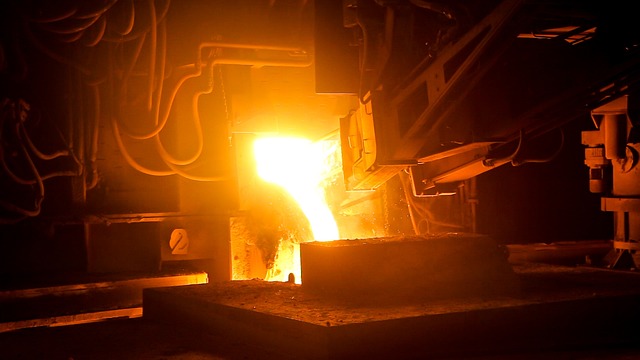
Stahl herstellen – so geht’s
Stahl ist aus unserem Leben nicht wegzudenken. Er findet Gebrauch in unterschiedlichsten Sphären wie etwa:
- Autoindustrie;
- Schienenproduktion;
- Straßenbau;
- Bauindustrie (Stahlhallen, Stahlrahmen verstärken Gebäude);
- Energieerzeugung- und Übertragung.
Das sind aber nur die, sozusagen, globalsten, bedeutendsten Bereiche. Aber auch solche Kleinigkeiten, die im alltägliche Gebrauch permanent funktionieren, wie z.B. Blechdosen oder Münzen bestehen ebenfalls aus Stahl.
Aber Stahl heißt nicht gleich Stahl. Der Herstellungsprozess verbessert sich ständig, es entstehen immer neuere Stahlarten- und Generationen, die langlebiger, flexibler und umweltfreundlicher als ihre „Vorfahren“ sind. Kein anderes Metallmaterial verfügt über derart breite Vielseitigkeit.
Aktuell produziert man eine große Anzahl an Stahlsorten. Neben dem Kohlenstoffgehalt unterscheiden sich diese Sorten auch durch das Vorhandensein von Legierungszusätzen, welche die Korrosions-, Kälte- und Hitzebeständigkeit erhöhen. Die am meisten verbreiteten Legierungselemente sind:
- Chrom, dank dem Stahl hart, korrosionsbeständig und elektrisch resistent bleibt;
- Nickel, dessen Wirkung auf Stahlmaterialien für deren Zähigkeit und Duktilität sorgt;
- Mangan – härter den Stahl, erhöht seine Verschleiß- und Schlagfestigkeit;
- Wolfram ist für Härte und Hitzebeständigkeit des Stahls zuständig;
- Anadium verbessert die technologischen Eigenschaften, in erster Linie die Bearbeitbarkeit) von Stahl bei gleichzeitiger Beibehaltung hoher Festigkeit;
- Niob erhöht die Widerstandsfähigkeit gegenüber aggressiven Säuren usw.
Der volle Zyklus von Stahlerzeugung
Beim vollständigen metallurgischen Zyklus der Stahlerzeugung entstehen aus natürlichen Rohstoffen durchs Walzen fertige Metallwaren eines bestimmten Profils, die man Walzprodukte nennt. Dieser Prozess umfasst drei Produktionsstufen, wobei das Endprodukt jeder einzelnen Stufe zum Halbzeug fürs Produkt der nächsten Stufe wird. So sieht es konsequenterweise aus:
- Herstellung von Roheisen;
- Stahlherstellung;
- Herstellung von Walzprodukten.
Normalerweise klassifiziert man diverse Stahlsorten sowohl nach ihrem Verwendungszweck (ob man sie z.B. zur Herstellung von Maschinenteilen oder Werkzeugen anwendet) als auch nach ihrer chemischen Zusammensetzung:
- kohlenstoffhaltig – sind am populärsten und günstigsten ;
- niedriglegiert (bis 2,5%);
- mittellegiert (bis 10 %);
- hochlegiert (über 10 %).
Legierte Stahlarten sind teurer. Man setzt sie dort ein, wo eine erhöhte mechanische, chemische und thermische Beständigkeit erforderlich ist.
Je nach der Spezifik des Zusatzstoffs variieren die Stahlsorte auf vielfältige Weise. Diese oder jene Mischung beeinflusst die technischen Eigenschaften des Stahls, weil jeder Tätigkeitsbereich seine eigenen Anforderungen stellt. Diverse Zusätze unterschiedlicher Konzentration helfen dem im Prozess der Stahlherstellung entstandenem Endprodukt, diese Anforderungen branchenentsprechend zu erfüllen.
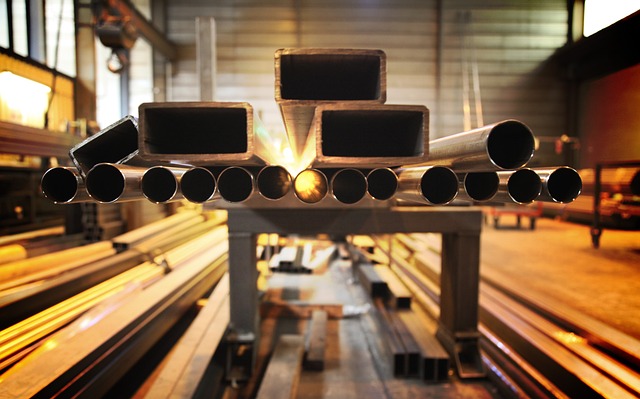
Herstellung von Stahl – unsere Schlussfolgerungen
Derzeit verwendet man in der Stahlindustrie drei Hauptmethoden zum Schmelzen von Stahl: Offenherd, Sauerstoffkonverter und Lichtbogenofen. Unten besprechen wir jedes dieser Verfahren etwas genauer:
- Offenherd – die Methode hat 1864 der Franzose Pierre Martin entwickelt, der einen regenerativen Flammenofen für die Stahlherstellung einsetzte. (In manchen Sprachen nennt man solche Mechanismen daher „Martinöfen“). Heutzutage ist diese Methode durch produktivere Verfahren beinahe völlig ersetzt.
- Sauerstoffkonverter – bei dieser Technologie leitet man den Sauerstoff durch geschmolzenes Eisen, das sich in speziellen birnenförmigen Behältern befindet. Dabei unterliegen alle Arten von Verunreinigung sowie der Kohlenstoff dem Oxidierungsprozess. Am Ende des Schmelzvorgangs kippt der Konverter und gießt das Metall in eine dafür vorgesehene Pfanne, die Schlacke dagegen in eine extra Schlackenschüssel. Die Konverter selbst bestehen ebenfalls aus Stahl und sind von innen mit feuerfesten Steinen ausgekleidet. Die Zufuhr vom Sauerstoff kann entweder von unten oder von oben erfolgen. Zusammen mit geschmolzenem Eisen und Altmetall (bis zu 10%) führt man dem Konverter schlackenbildende Bestandteile (Kalk, Feldspat usw.) zu. Schlacke sind nötig, um schädliche Schmelzreste – vor allem Phosphor und Schwefel – zu sammeln.
- In einem Lichtbogenofen erfolgt das Schmelzen des Metalls aufgrund der Wärme, die durch den Lichtbogen erzeugt wird. Der Letztere bildet sich zwischen den Elektroden und der Metallmischung. Die Lichtbogen-Stahlschmelzöfen unterliegen keinen Beschränkungen, wenn es um die Beschickung von Metallschrott geht. So ermöglichen sie eine genaue Kontrolle des Temperaturwechsels sowie der chemischen Zusammensetzung der Legierung. Entwickelt hat man diese Öfen während des Zweiten Weltkriegs, als eine große Nachfrage nach hochwertigen legierten Stahlsorten bestand.
Für die Herstellung von nicht legiertem Baustahl verwendet man solche Zusammensetzungen wie Stahlschrott (bis zu 90%), Gusseisen in Barren (etwa 10%), Koks (zum Ausgleich des aus der Schmelze ausgebrannten Kohlenstoffs) und Kalk (zur Schlackenbildung).